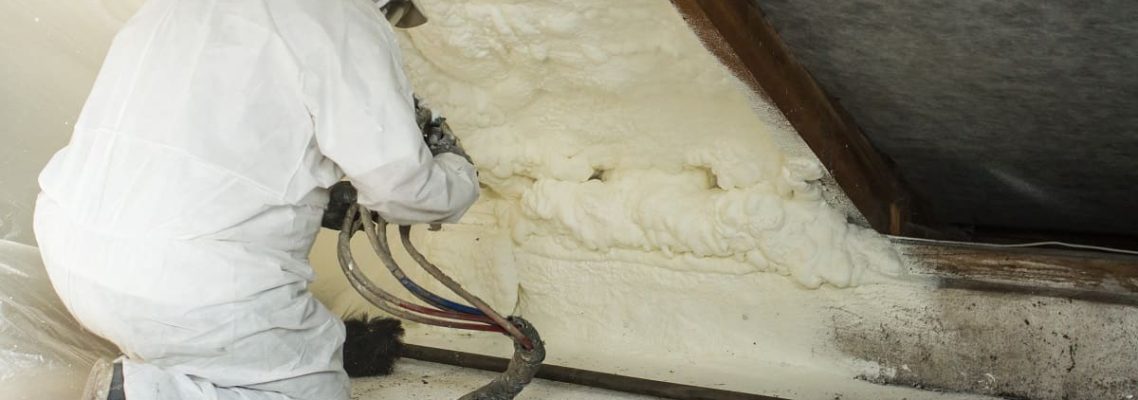
DIY vs Pro Crawl Space Insulation: Oak Springs Guide
July 1, 2025
You’re scrolling through YouTube at 2 AM, watching someone make crawl space insulation look ridiculously easy. The narrator’s confident voice promises you’ll save thousands while learning a valuable skill. But here’s the thing about Oak Springs homes – that coastal Virginia humidity changes everything.
Most homeowners start with the best intentions. They see the potential savings, feel that surge of DIY pride, and honestly believe they can tackle their crawl space in a weekend. For Oak Springs residents seeking reliable insulation solutions, the reality proves far more complex than those cheerful tutorial videos suggest.
The numbers tell a different story. About 85% of homeowners who attempt DIY crawl space insulation end up calling professionals to fix their mistakes. That’s not because they lack intelligence or motivation – it’s because coastal Virginia presents unique challenges that even experienced DIYers struggle to handle.
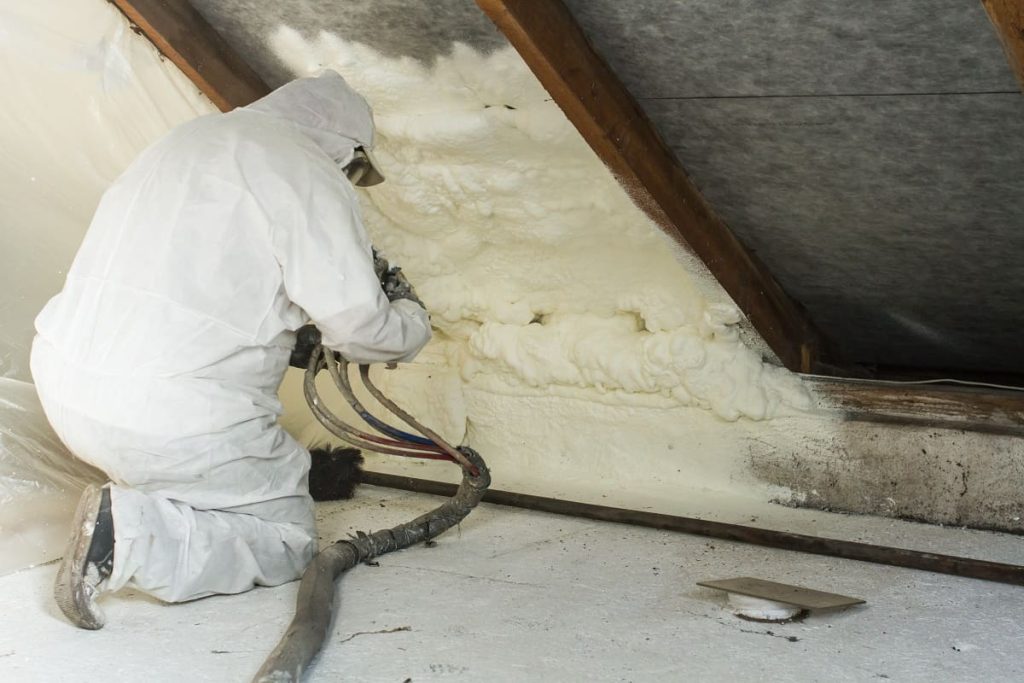
Content
The DIY Temptation: Why It Seems So Appealing
The initial math looks compelling. Materials for an average Oak Springs home run between $2,000 and $4,000, while professional installation might cost $5,000 to $15,000. That difference catches attention fast.
There’s also something deeply satisfying about improving your own home with your hands. The sense of accomplishment, the control over timing, the learning experience – these factors make DIY projects genuinely appealing. Some homeowners have succeeded with crawl space insulation, though they’re typically the exception rather than the rule.
The physical reality hits differently than expectations. Crawling through tight, uncomfortable spaces for hours while wearing safety gear in Virginia Beach’s humidity becomes exhausting quickly. Most crawl spaces harbor unpleasant surprises: mold, pests, poor air quality, and structural issues that weren’t visible from the access point.
Oak Springs’ Coastal Challenge
Here’s where those YouTube tutorials fall short – they don’t account for Oak Springs’ unique environment. The area maintains 60-80% humidity year-round, with salt air affecting material performance and seasonal flooding creating additional moisture concerns.
Standard fiberglass insulation, popular in DIY projects, absorbs moisture like a sponge in these conditions. Within months, it becomes a breeding ground for mold and mildew. The vapor barriers require specific thickness – 6-mil minimum, though 20-mil performs better in coastal conditions – and must resist UV degradation from reflected sunlight.
Ground moisture from proximity to water bodies creates additional complications. The soil stays damp longer, foundation walls wick moisture upward, and temperature differentials between seasons create condensation issues that dry-climate tutorials never address.
Common DIY Disasters
The most expensive mistakes happen with moisture control. Homeowners install insulation over existing moisture problems, trap water vapor behind improperly installed barriers, or skip the drainage assessment entirely. These errors lead to wood rot, structural damage, and mold growth that costs far more than professional installation.
Material selection errors compound the problem. Using wrong insulation types for coastal conditions, insufficient coverage leaving thermal bridges, and poor sealing around penetrations create long-term performance issues. Building codes require specific termite inspection gaps that DIYers often miss, creating compliance problems during home sales.
The consequences extend beyond immediate costs. Trapped moisture creates perfect conditions for mold growth, which affects indoor air quality and family health. Structural damage from wood decay threatens the home’s integrity, while pest infestations in improperly sealed spaces create ongoing problems.
Professional Advantages
Professionals bring comprehensive assessment capabilities that DIYers lack. They test moisture levels, identify sources, evaluate structural conditions, and understand how HVAC systems integrate with insulation performance. This knowledge prevents problems rather than creating them.
Access to superior materials makes a significant difference. Commercial-grade vapor barriers come with warranties, specialized insulation products handle coastal climates better, and professional-grade sealants provide long-term performance. The equipment required – spray foam rigs, cutting tools, safety gear – represents substantial investment for one-time use.
Installation quality affects long-term performance dramatically. Professionals complete jobs in days rather than weeks, provide warranty protection on materials and labor, and offer follow-up service when issues arise. Their technique ensures complete coverage without gaps or thermal bridges.
The Real Cost Analysis
DIY hidden costs add up quickly. Tool rental or purchase, multiple material trips with waste, permit fees, and inspection costs often double initial estimates. Time investment typically exceeds 40 hours for average projects, and mistake correction can cost more than professional installation.
Professional services in Oak Springs typically range from $5,000 to $15,000, depending on space size and complexity. This includes warranty coverage, proper installation techniques, and materials designed for coastal conditions. Energy savings of 15-25% on utility bills help offset costs over time, while proper installation increases home value.
Long-term financial impact favors professional installation. Quality work lasts 15-20 years, while DIY failures often require complete re-work within five years. Insurance implications of improper installation can affect coverage for moisture-related damage.
When DIY Might Work
Limited scenarios exist where DIY makes sense. Small, accessible areas without moisture issues, homeowners with relevant construction experience, and supplemental work to existing professional installation represent the few success stories.
Prerequisites for DIY success include extensive research, proper safety equipment, realistic timeline expectations, and professional consultation for complex issues. Even then, coastal Virginia’s conditions stack the deck against DIY success.
Making the Right Decision
Honest self-assessment helps determine the best approach. Previous insulation or construction experience, comfort working in confined spaces, understanding of building science principles, and available time all factor into success probability.
Project scope evaluation matters equally. Large or complex crawl spaces, existing moisture or structural issues, local building code requirements, and integration with other home systems all favor professional installation.
Universal Insulation Doctor has seen countless Oak Springs homeowners attempt DIY projects only to call for professional help when problems arise. The coastal climate demands expertise that goes beyond basic insulation knowledge.
The Bottom Line
Oak Springs homeowners choose professionals because the risks outweigh potential savings. Coastal climate demands expertise, mistakes cost more than professional service, and warranty protection provides peace of mind. Long-term performance and energy savings justify the investment.
The smart approach involves professional consultation even when considering DIY. Free inspection services help identify potential problems, provide realistic cost estimates, and offer guidance on whether DIY makes sense for specific situations.
Your home represents your largest investment. Protecting it with proper crawl space insulation requires understanding coastal Virginia’s unique challenges and having the right tools, materials, and expertise to address them effectively. Sometimes the best DIY decision is knowing when to call the professionals.
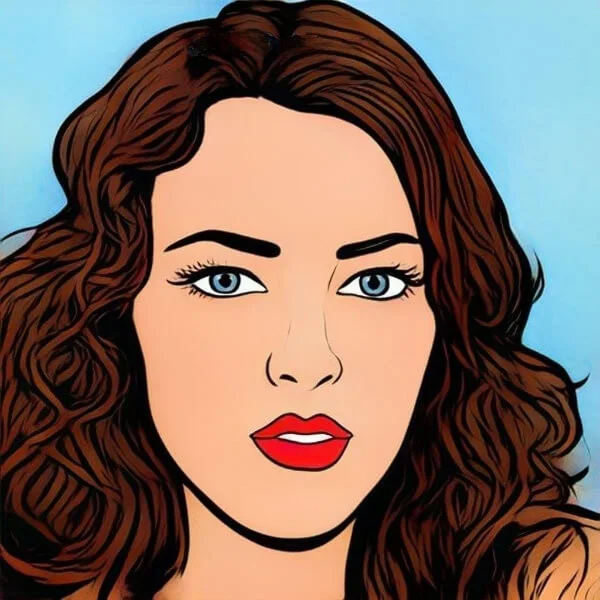
Christine Kelley is a dedicated home blogger who has been blogging for over six years. She covers everything home related. Christine also loves writing posts about her travels to Europe with her husband and two children.